Cable Conductors
(Signal Core)
Engineered : Core Engineering Principles
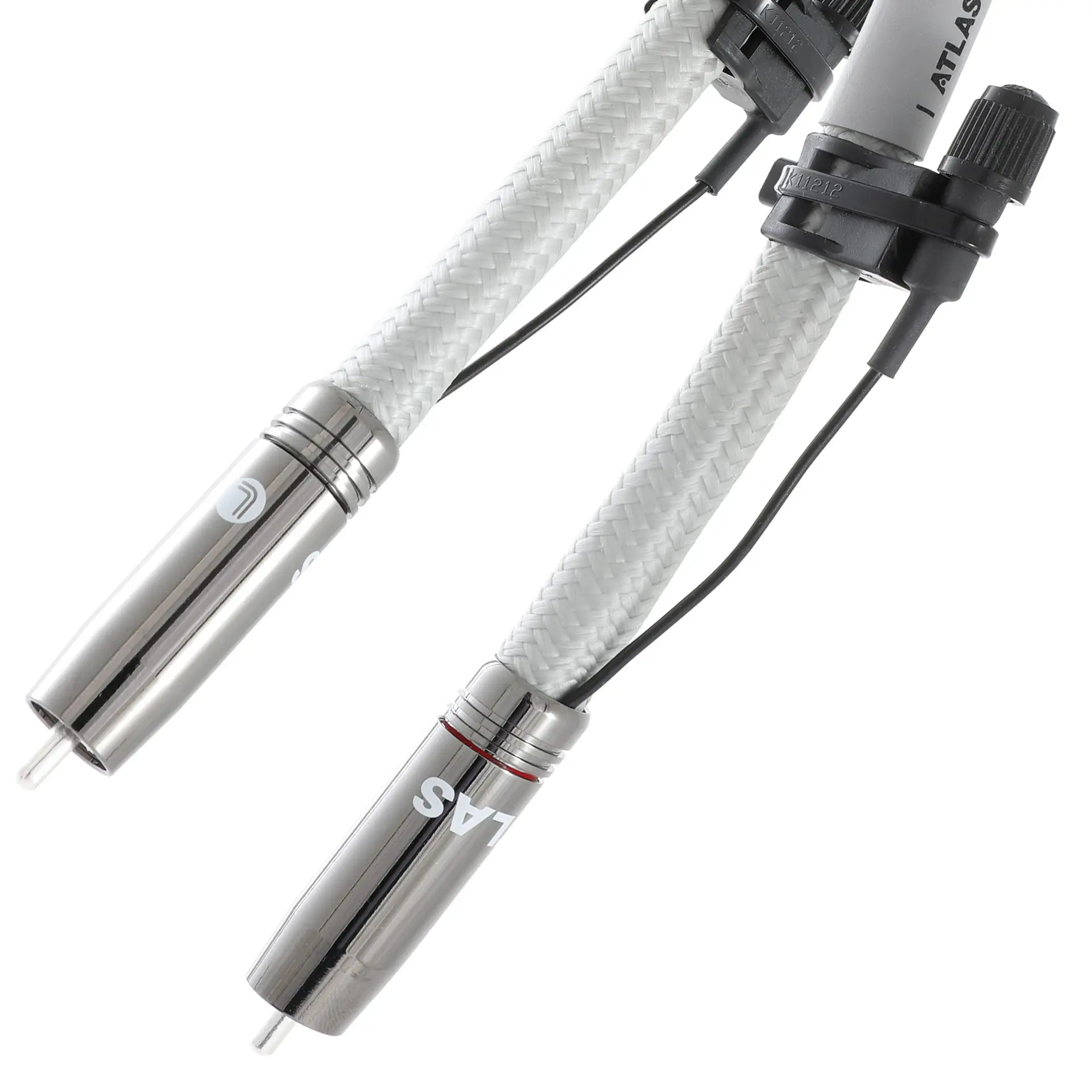
The different conductor types typically used in audio applications.
Tough Pitch Copper (TPC)
Tough Pitch Copper (TPC) is the name given to unprocessed copper: the type usually employed in general purpose cabling such as power leads and many inexpensive audio cables. TPC is melted once and formed into a cylindrical conductor (wire) which is then allowed to cool. This wire is then repeatedly drawn to reduce it to the desired diameter.
TPC contains somewhere between 300 and 500 ppm of oxygen and other impurities, which is considered far too high for serious audio applications, tending to cause a loss of fine detail, resulting in a dull sounding system.
Oxygen Free Copper (OFC)
Oxygen free copper was developed in Japan around 1975 as it became increasingly apparent that sound quality was related to the quality of copper and the processing used during cable manufacture.
OFC is produced through an extrusion process which takes place in an oxygen-free-inert-gas atmosphere. This leads to a reduced oxygen content (10 ppm) when compared to TPC and an improvement in conductivity which typically measures in at between 0.5% and 2% greater than TPC. The OFC process therefore produces a much higher quality audio cable than the TPC process. High purity conductors sound clearer than their unprocessed (TPC) counterparts because there are fewer crystal boundaries present to cause signal degradation.
Linear Crystal-Oxygen Free Copper (LC-OFC)
Also around 1975, Hitachi developed their own method for reducing grain or crystal boundaries. LC-OFC was Hitachi's patented process and their exclusive product. After extrusion, the copper wire is re-heated, or annealed, which reduces impurities between the crystal boundaries as the copper crystal grows and leads to a longer grain length. A typical crystal (or grain) in a 1mm diameter LC-OFC conductor is 130 mm long compared to only 4mm (typically) long in TPC or OFC conductors. Atlas cables don’t use LC-OFC, we get better results from OCC.
Ohno Continuous Casting Copper (OCC Copper)
In 1985, Professor Ohno, from the Chiba Institute of Technology, developed his patented method for the extrusion of a grain-free copper wire. (Technical papers are available from the Japan Inst. Metals and from Chapman & Hall, publishers.)
When a pure metal solidifies, its crystals grow in a specific geometrical pattern (typical to that metal) emanating from a nucleus, rather like the dendritic growth pattern of a tree. The size of the metal crystals grown can be varied by repeatedly annealing metal such as is done in the LC-OFC process. The structure of a strand of copper may be likened to that of a bag of sugar. Every grain of sugar has a crystal boundary. In a conductor, these crystal boundaries (potential barriers) act as a non-linear resistance to the flow of electric current. It follows that, the fewer the boundaries, the less the effect there is on an electric signal as it propagates from one end of the conductor to the other. Atlas cables such as the Arran and Mavros use OCC copper, whereas the top of the range Asimi uses pure OCC silver.
The Ohno continuous casting method re-heats the extrusion as the molten copper is forced out of the mould and very slowly and gradually draws the grain or crystal down the conductor‘s length, creating a ‘single crystal structure.’ Actually, because no copper is 100% pure, there will always be a few boundaries produced by impurities. The frequency of boundaries created are quite insignificant. A typical crystal in a copper conductor drawn to 0.3 mm diam. using the OCC process is 125.00 metres long!
The benefits are obvious, with almost no crystal boundaries, the audio signal is no longer impeded down the copper wire and more information and detail is delivered faithfully to the receiving equipment.
Silver-plated Copper
Seemingly good high-frequency dynamics are characteristic of silver-plated copper conductors. Silver-plated copper can appear to make a dull-sounding system come to life, but at the expense of good quality bass or low frequency delivery. Silver-plated copper cables can also prove fatiguing and irritating over prolonged listening periods.
Silver-plated copper, or cables employing two materials of differing resistance, are best avoided for audio interconnects and speaker cables.
While it’s a cheap method for producing an audio interconnect that may initially sound exciting but we’d not choose to use it in our systems at home – at Atlas Cables we refuse to employ silver-plated copper for analogue audio applications; the biggest complaint we hear from callers is they’ve bought silver-plated cables and their system is excessively ‘bright.’ Better results can be achieved with high-quality processed copper and superior dielectrics.
Pure Silver
Silver, with its lower resistivity, is a better conductor than copper, but any conductor, whether silver or copper, must have a reasonable cross-sectional area when used for audio applications. Silver is much more expensive than copper and, in order to keep costs within reason, the cross sectional area of silver audio cables are often compromised and the resulting sound is ‘bass light.’
Good silver cables are, however, fast, dynamic and seamless through the audio spectrum and provide exceptional detail and instrument resolution. Atlas Asimi cables employ OCC silver conductors and in the case of the Asimi speaker cable, these are a substantial 5.0 sq mm in overall size in order to provide wide bandwidth and superior definition.