Cable Design Objectives
Engineered : Core Engineering Principles
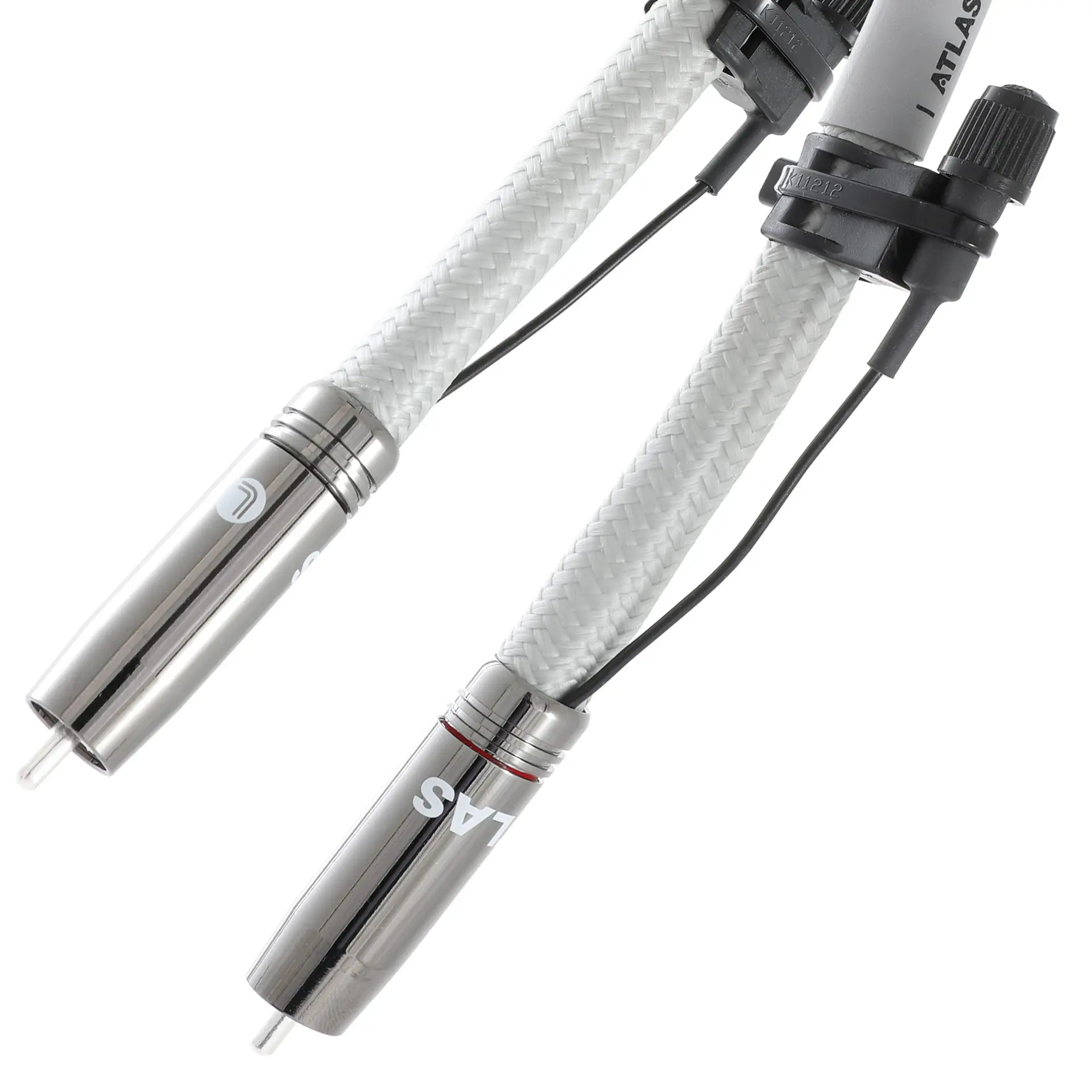
When we design any analogue or digital cable we start by considering five main elements : the conductor material; the dielectric (insulation) properties, the connectors, screening/shielding and the overall construction and manufacturing process.
Overview
Our preferred conductor material is OCC (Ohno Continuous Cast) copper or silver which has no discontinuities in the signal path. Depending on the application the conductor can be a single wire or a bunch of wires of the same diameter or a mixture of diameters.
In theory an ideal cable will simply comprise a pair of pure conductors in free air, although in practice the conductors need to be covered by an insulating material, normally a thermoplastic. This is to stop the two wires from ‘shorting’ together as well as protecting the conductors surface from corrosion – copper and silver being particularly vulnerable in this respect. These changes to the ideal conductors now compromise its theoretical performance, instead of free air between the conductors there are now two insulating tubes forming a dielectric, which effectively slows the potential propagation speed of the cable.
What do we mean by the ‘speed’ of a cable? Well, the most common term in use is the Velocity of Propagation (VOP): the speed at which the signal travels down the conductor. We have a series of Technical Papers available if you wish to know more. This measurement is made using a technique called TDR (Time Domain Reflectometry). The TDR technique is based on the fact that if you fire an impulse down an open-ended cable the impulse will be reflected back by the open end and return back to the beginning. This test gives us the VOP.
All dielectrics slow down the signal velocity, the best slow least. The faster signal provides wider bandwidth, so a faster cable delivers more accurate information. The latest Atlas cables with Microporous PTFE/ extruded FEP or foamed polyethylene dielectrics (PEF) are very fast, they have wider bandwidth and therefore more open, accurate and natural music.
At Atlas our mission is ’connecting customers to the music that they love.‘ We don’t place barriers in the signal path, nor do we skew the signal by using conductor materials with different characteristics (e.g. silver-plated analogue cables), we make wide-bandwidth cables that allow the transmission of more information.
Cable Performance Parameters
Capacitance
Lower capacitance interconnects and speaker cables are preferable to high capacitance ones which may prove a mismatch for some older amplifiers. Any frequency distortion or amplifier instability which could result from using high capacitance cables is primarily not caused by the cable itself, but rather by using the cable between inappropriate components.
The capacitance of a cable is determined by conductor geometry and the dielectric constant of the insulation employed. Although the vast majority of cables available use some form of low-cost PVC, it should be avoided for audio signal path applications. Better alternatives are polyethylene (PE), foamed polyethylene, polypropylene (PEF), low temperature PTFE (FEP) or the new Atlas microporous PTFE. The foaming process reduces the dielectric constant, thereby stabilizing the frequency characteristics. Any insulation between two conductors creates a capacitor which stores and later releases energy. The less energy absorbed, the better the signal velocity (speed) will be. Within the audible audio spectrum, the magnitude of capacitance, together with conductor resistance, principally governs the level of frequency attenuation.
Impedance
In the digital domain, it is of fundamental importance that the correct type of cable is employed in order to match the signal source impedance into the load presented by the receiving equipment.
The most appropriate cable is an ‘asymmetrical’ or co-axial, unbalanced design, usually of 75 Ohms Characteristic impedance. In the digital domain, there should theoretically be no deletion of digital information.
In practice however, cables sound different, so clearly some loss of information is taking place. RCA phono plugs are most commonly used, though BNC plugs are superior with regard to characteristic impedance matching. Most RCA plugs grip the cable with a compression gland (collet) or grub screw in the side of the plug which is screwed into the cable. This simple mechanical step dramatically affects the characteristic impedance and the ability of the receiver to extract the data in the most efficient manner.
The co-axial or asymmetrical cable uses going and return conductors which are not electrically equivalent, giving rise to often used descriptor ‘unbalanced.’ The return path acts as a screen and a barrier to Radio Frequency Interference (RFI). To improve the quality of digital and high frequency cables, a second shield and an additional aluminium foil are often employed.
To achieve a 75 Ohm characteristic impedance, a manufacturer typically selects a diameter for the central conductor which then determines the correct separation between the centre (or going conductor) and the screen (or return conductor). If that separation is reduced by a plug compressing the cable, the cable’s impedance will be altered, creating reflections inside the cable causing signal deformation (the rise or fall time of the square wave signal is changed) and unwanted jitter.
A typical RCA plug can reduce a cable’s impedance from 75 to around 45 Ohms! Atlas use RCA plugs which don’t compress the cable.
Shielding
Cables are shielded to protect sensitive signals from external noise.
There are two generally two types of shield, one to reject electrically induced noise, the other to reject magnetically induced noise. The rejection of electrically induced noise requires the shield to be made of a metal with a high conductivity (since RFI rejection requires ‘shielding’ currents to be able to flow easily in the shield.
In an unbalanced interconnect, the shield also acts as the signal return path, while in a pseudo-balanced RCA configuration the shield and return paths are two identical conductors surrounded by a wrapped/woven screen, with the shield left open at one end. This makes pseudo-balanced interconnects directional by manufacture.
A cable could be wrapped around a ferrite core (iron etc.) to maximize the rejection of magnetic fields. Interconnects incorporating such a shield are bulky, this method of magnetic field rejection is not generally used on hifi. To reject magnetic interference in hi-fi applications, it is usually sufficient to twist the insulated conductors together to form what is known as a twisted pair.
Nowadays technologies such as ‘High Definition Audio’ can produce audio signals well beyond the 20kHz value which was typically considered to be an adequate cut-off frequency for HiFi systems. In response to this, some loudspeaker producers are meeting the latest demands for high frequency extension with highly sophisticated tweeters capable of reproduction well above 20kHz. A few speaker manufacturers provide a ground contact on the speaker so that a drain wire can be connected to reject RFI which can otherwise become an audible problem at frequencies in excess of about 20kHz.
It’s not only the quality/quantity of shielding but also the method of terminating the screens to maximise the Rf performance. At Atlas we utilise a special technique called ’Dual-Drain‘ which not only eases the manufacturing process and maintains the screen integrity but also maximises the screen efficiency to eliminate unwanted noise.