Cold-Weld Crimp
(Making the right connection.)
Engineered : Core Engineering Principles
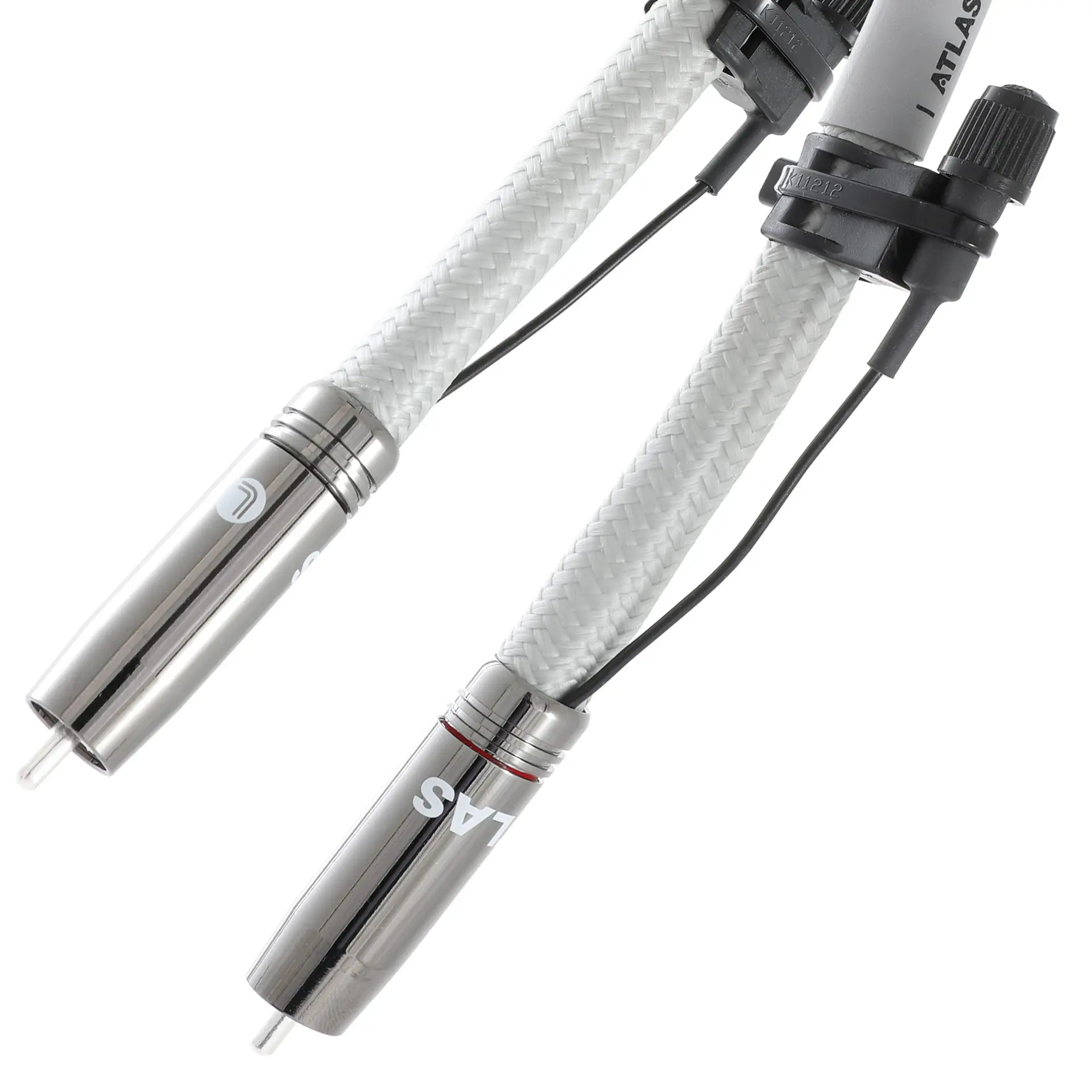
Our objective is a smooth, uninterrupted signal path which behaves as one continuous entity, with the minimum of ‘breaks & barriers’ in the signal path.
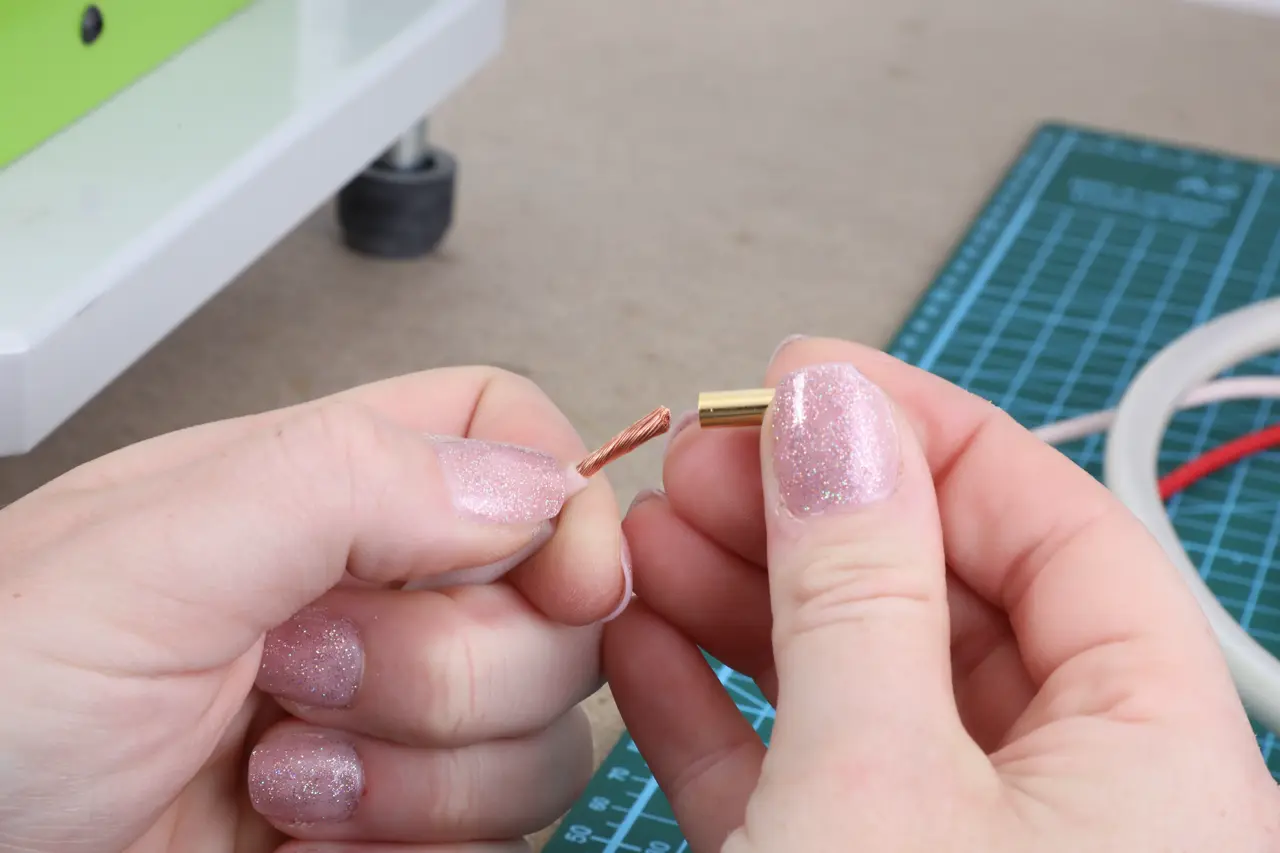
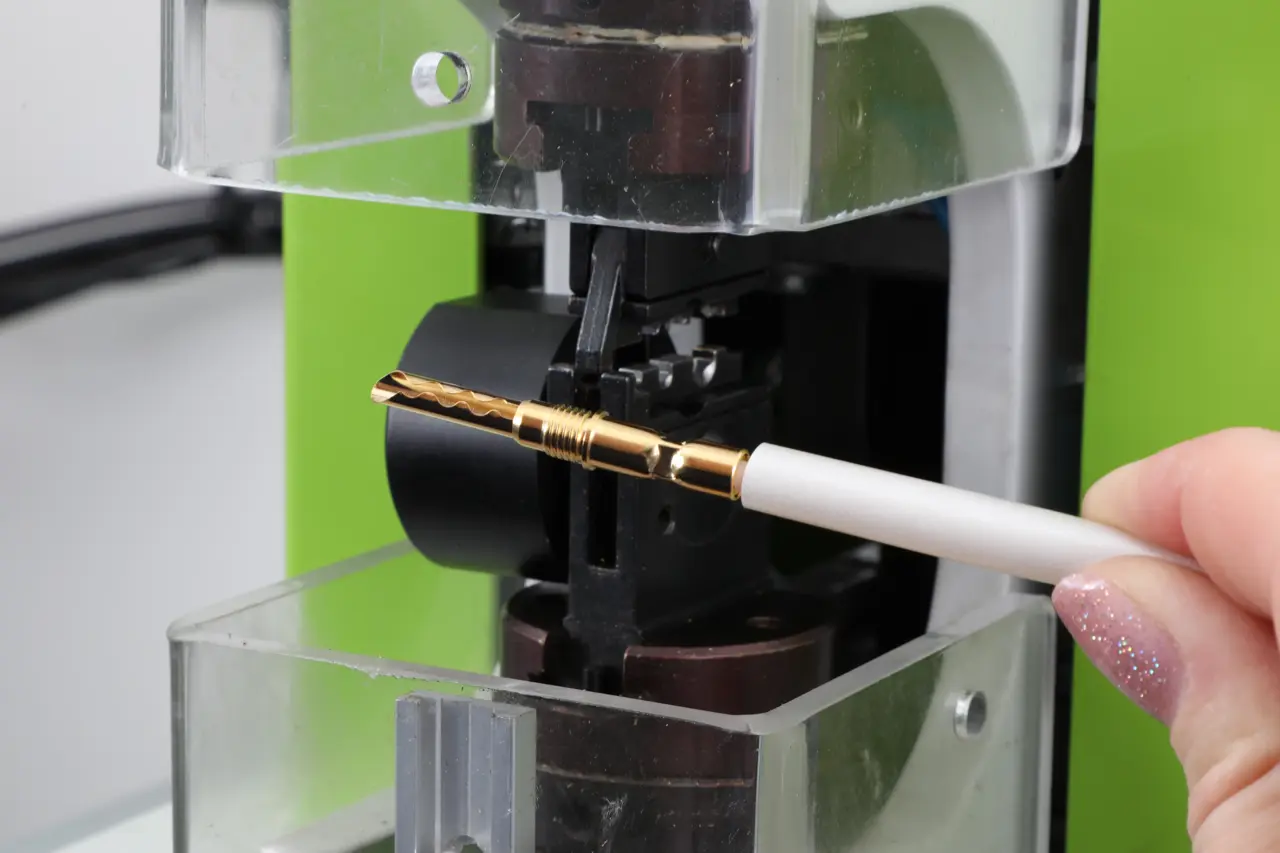
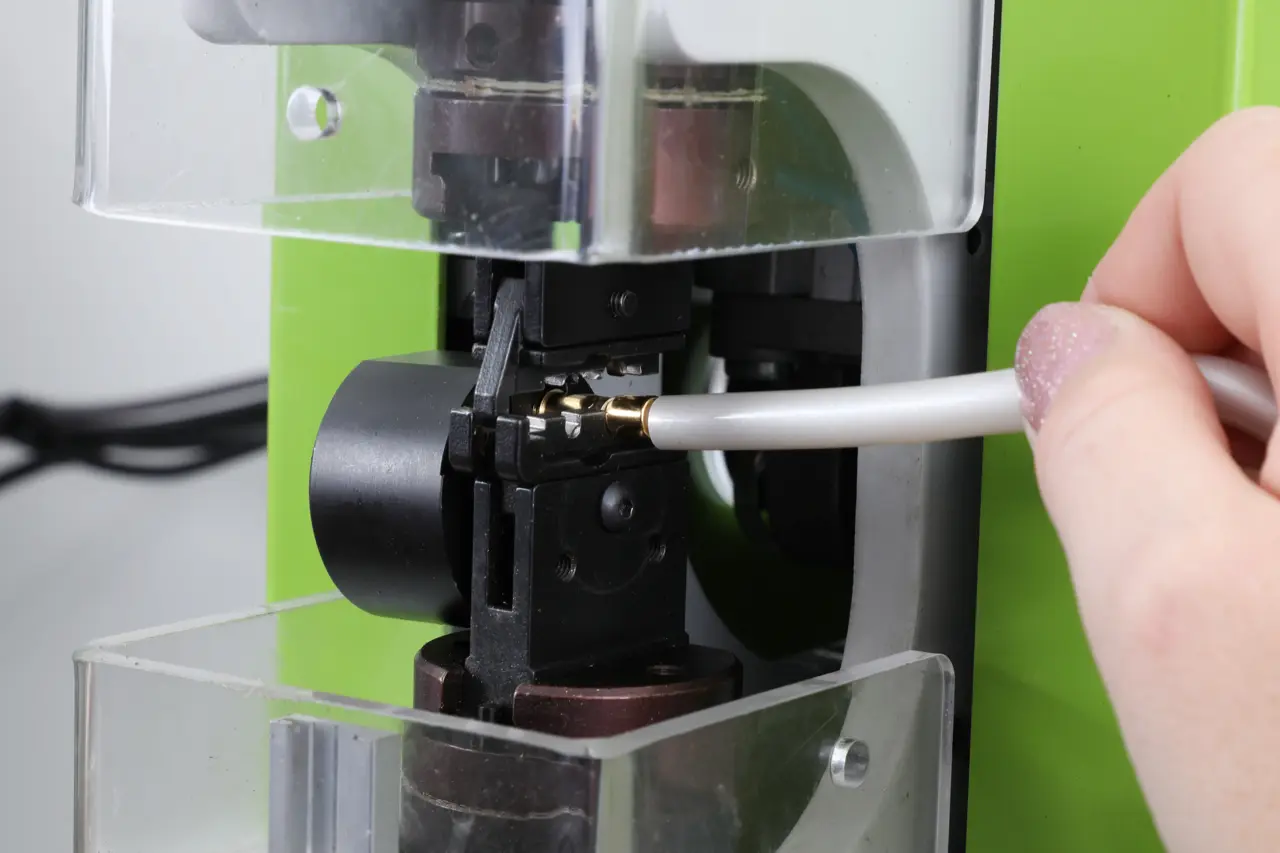
The Process
We have invested in machinery to quickly and efficiently perform a number of the key stages in our manufacturing process, including precision-crimping of connectors on all types of cable.
We also have a number of identically calibrated hand-tools — there are times when there’s no substitute for the experience of a skilled operator.

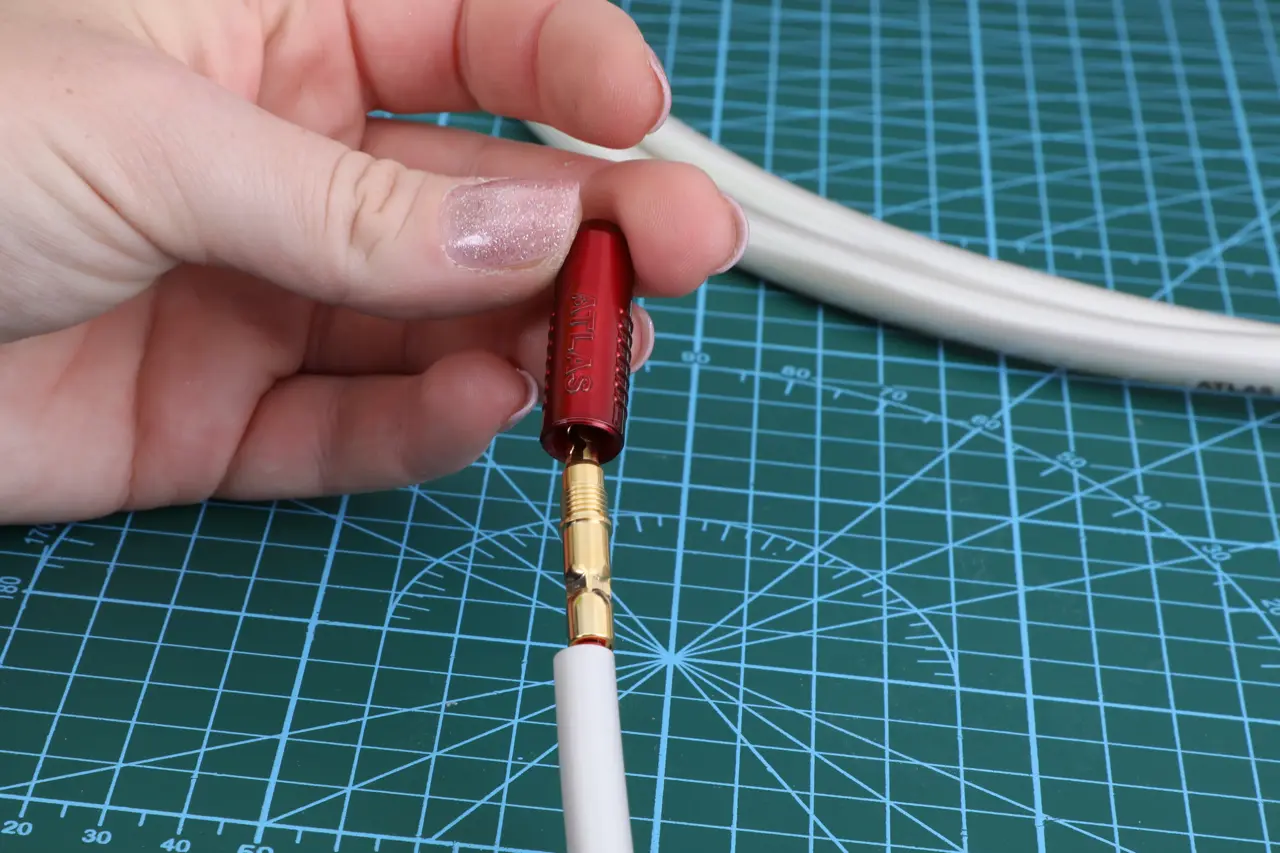
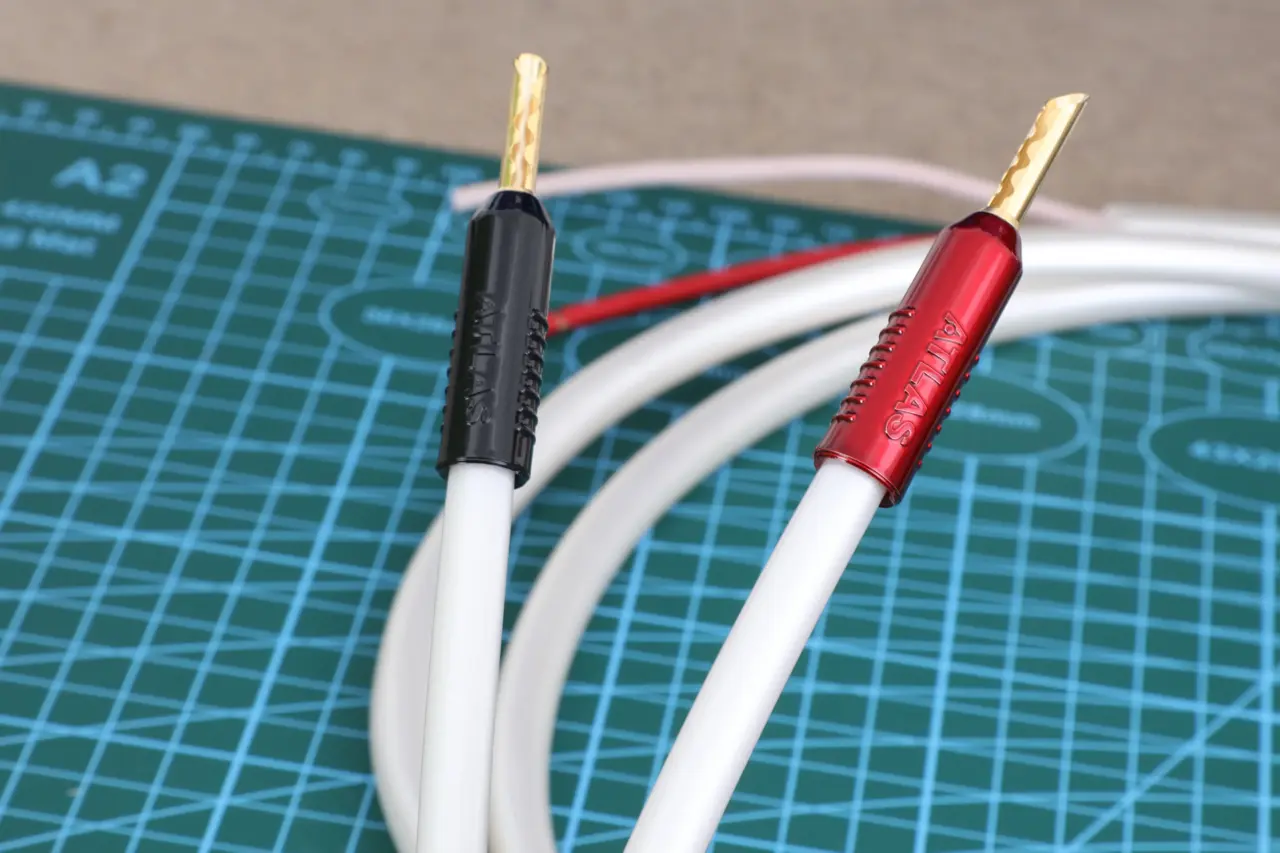
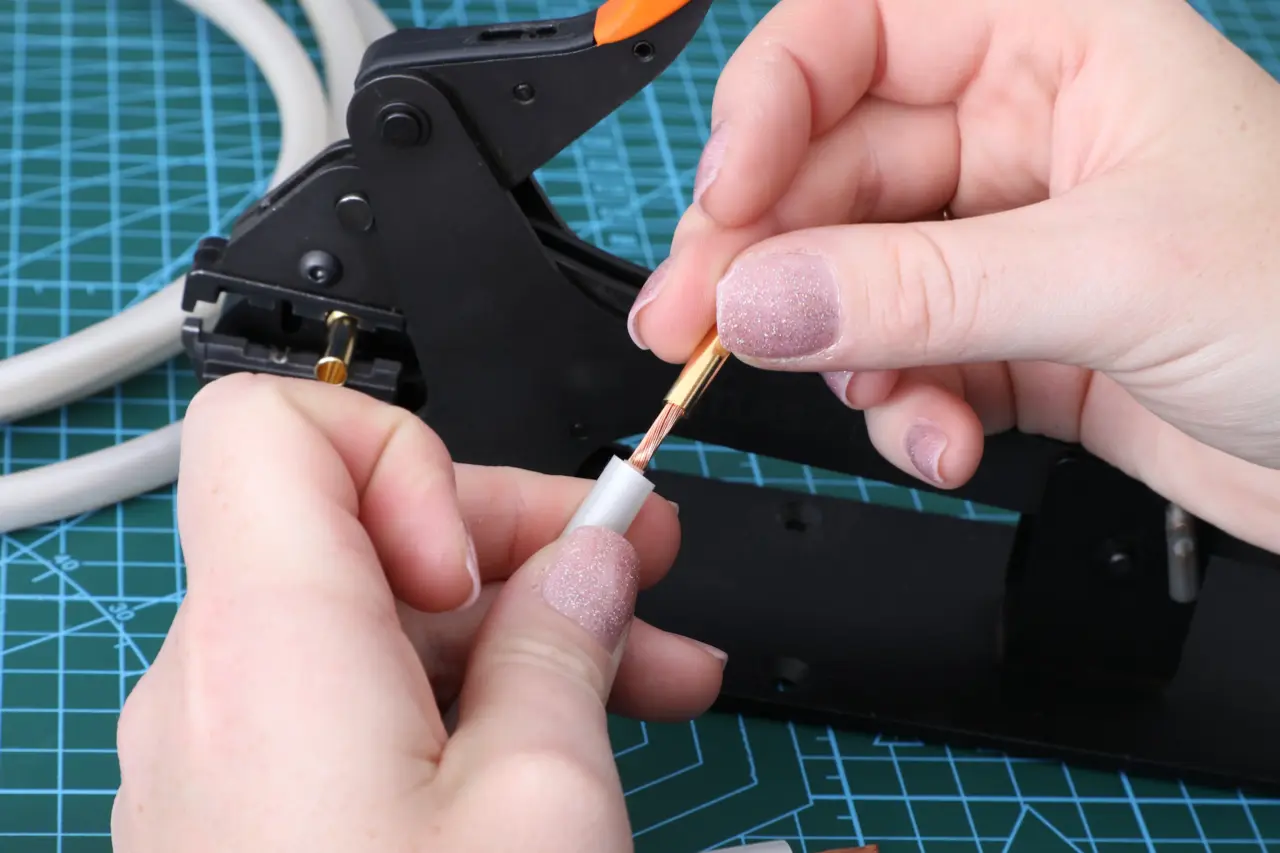
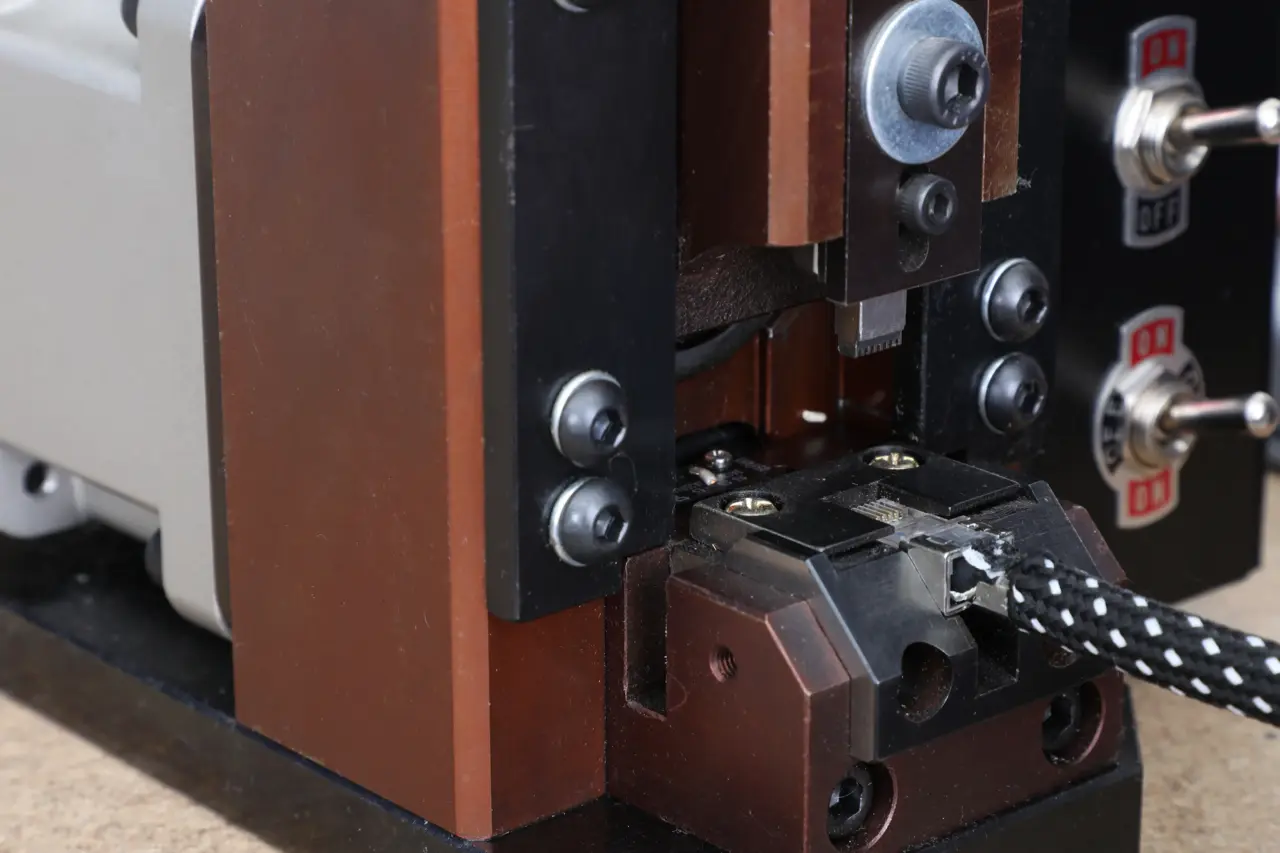
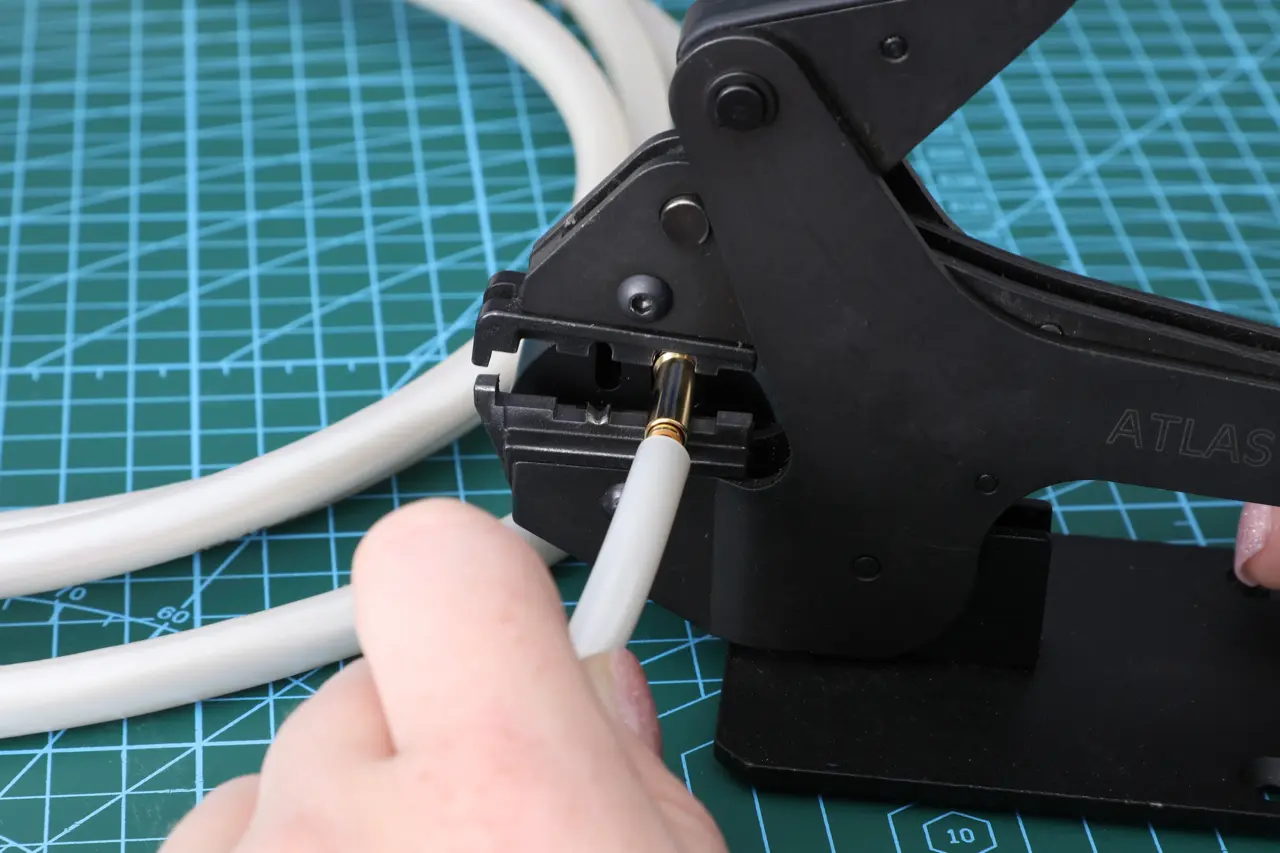
Cold-Weld Precision-Calibrated Crimp
We firmly believe there should be the minimum of ‘breaks & barriers’ in the signal path. To this end for example, the pins on our connector plugs will typically be of the same material as the cable conductor, ie. a cable using a OCC Copper conductor will have OCC Copper signal pins.
We consider a precision-calibrated cold-weld connection (where physically possible) to be superior to soldered joints or screw connections. Solder typically introduces an unwanted material barrier and a degree of inconsistency. Screw terminations typically distort/damage the conductor and/or dielectric, adversely affecting the measured characteristics of the cable.
In a cold-weld (solder-free) connection, the metal of the connector plug and the wire are squeezed together under a calibrated pressure to form a robust, consistent, air-tight metal to metal contact with no deformation of the cable dielectric. The result is a smooth, uninterrupted signal path which behaves as closely as possible to one continuous entity.